物理气相沉积PVD Ti/TiN涂层提高冷冲模具寿命研究
发布时间:2020-05-26
1、前言
随着汽车工业的迅速发展,汽车配套零件的需求量大幅度增加。其中,冷加工件的质量、产量和生产成本往往取决于冷作模具的工作条件及有效使用寿命。例如冷冲模具“控制臂翻边凸模”(Cr12MoV),在大批量的生产过程中,大约经过2500次冷冲后就会导致冷冲件尺寸不合格造成报废。经失效分析其主要原因是模具的摩擦学性能差,低的耐磨性和耐粘着性容易使模具的翻边圆角和翻边直壁磨损。为提高冷作模具使用寿命,在冷作模具上沉积TiN等硬质涂层是一有效途径,采用离子氮化+物理气相沉积硬质涂层则可进一步提高涂层与基体的结合强度及涂层的耐磨性,但由于模具工作条件的复杂性,所以在这方面的应用报道还比较少。
2、试验方法和内容
2.1 试样准备
以Cr12MoV为基体材料,加工成30*3*7mm3规格的试样,经高淬高回热处理(1100℃真空淬火和520℃×1.5h两次回火),硬度为61HRC。再经砂纸研磨(从粗砂到03#),最后用W2.5金刚石研磨膏抛光。试样在涂层前经严格的清洗、除锈和除油。
双重处理涂层的制备工艺为:试样先在LD-8100型离子氮化炉中进行离子氮化,氮化温度500℃,氮化时间5h,真空度480~520Pa,工作电流30~40A。随后沉积Ti/TiN涂层(工艺同单一处理)。
2.2 涂层表面性能测试
用HX-1000显微硬度机,测定一系列载荷和(10g,25g,50g,100g,300g,500g,1000g)作用下的表面显微硬度值。并且,在HITACHS-570电子扫描显微镜(SEM)和光学显微镜(OM)下观察相应的显微压痕形貌,定性地分析涂层的表面承载能力及韧性。
用划痕试验评估涂层与基体结合状况。本实验采用半径为200μm金刚石划针(Stylus),以100N/min的加载速率连续加载,同时以10mm/min的速率划过试样表面,划痕位移为5000um,在划擦过程中,所加载荷由最初的10N增加到设定的60N。仪器同时记录摩擦力-载荷等曲线。此外,使用OM和SEM观察划痕形貌,由此定性地得出表面与基体的结合强度大小。
2.3 磨损试验
磨损试验在MM-200型国产磨损试验机上进行,以矩形涂层试样(30*3*7mm3)为上试样,表面等离子氮化的Cr12MoV钢(1200Hv)滚轮(Φ40mm×10mm)为对磨试样。磨损试验条件为:冲击式磨损(17次/min),转速200r/min(线速度为0.42m/s),20#机油润滑,载荷15kg,对磨0.5、1、3、6、9h,用磨损后的磨痕体积来衡量磨损量,计算公式为(1)式,同时利用OM和SEM观测磨损试样表面的磨痕形貌。

其中,V:磨痕体积,B:磨痕宽度,R:轮子半径,L:磨痕长度。
2.4 应用试验
3、结果和讨论
3.1 显微硬度试验
图1为表面硬度和载荷曲线,由图可见,未表面处理(高淬高回)试样的硬度值基本是不随载荷的变化而变化,而单一处理和双重处理试样的表面硬度则是随载荷的增加而减小,而且,在同样载荷下双重处理试样的硬度要比单一处理的高。同时从不同载荷下两种处理试样显微压痕形貌观测(见表1)结果发现,在较低载荷下(10g~300g),两类试样压痕周围和内部都无明显的裂纹出现,而当载荷较高(500g、1000g)时,单一处理试样压痕内部出现较多巢状裂纹(图2),而双重处理试样则较少。

显然,在Cr12MoV钢上沉积Ti/TiN涂层提高了材料的表面承载能力,特别是双重处理。这是因为在较小载荷(如10g)作用下,涂层-基体体系是以涂层的塑性变形为主的,承载能力主要来自于硬、韧的Ti/TiN涂层,所以单一处理和双重处理试样显示出高的显微硬度值,压痕周围无明显的裂纹出现。随着载荷的增大,基体对测试硬度的影响逐渐增大,双重处理试样因有基体离子氮化产生的强化层对涂层的有力支撑作用,因而显示出比单一处理试样更好的承载能力,而且,离子氮化减少了涂层-基体界面大的应力梯度,因此在高载荷如1000g下,压痕周围显示比单一处理试样少的巢状裂纹。
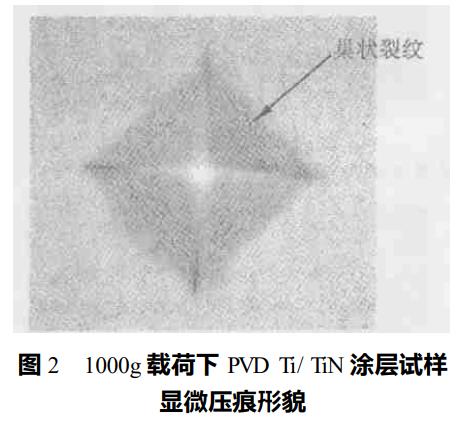
3.2 划痕试验
图3是单一处理和双重处理试样的划痕试验结果(摩擦力-载荷曲线)。可以看出随着载荷的增加,两类试样切向摩擦力基本都呈线形增加,单一处理的摩擦力更大一些,而且两者都没有出现摩擦力突然增大的峰值。单一处理试样摩擦系数大约保持在0.2左右(摩擦力-载荷曲线的斜率μ=F/N),而双重处理试样约为0.15。
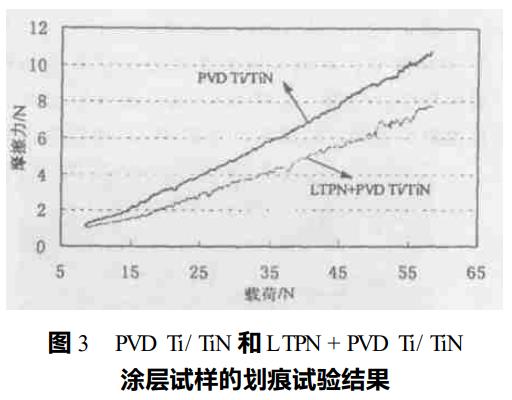
因摩擦力-载荷曲线没有显示出突然增大的摩擦力峰,显然,涂层还没有发生完全破坏,所以在Cr12MoV基体上沉积TiN涂层具有高的临界载荷(Lc),即Lc大于60N,而且可以预测双重处理有更高的临界载荷,因为离子氮化过程产生的离子溅射效应,会使基体表面产生微观的凹凸不平,因此增加了TiN涂层与基体的机械钳合作用;其次Fe、N、Cr、Ti内扩散层的形成和对界面应力梯度的降低,也对结合力提高起到影响;而且由于中间硬化层的效应,TiN裂纹的扩展只有在基材界面上才能进行,延长了裂纹移动路径,因此大大增加了TiN结合力。
3.3 磨损试验
为了更好地评价在Cr12MoV钢基体上单一处理和双重处理涂层的耐磨性,本实验采用高淬高回(未表面处理)Cr12MoV钢作为对比材料。表2是三种试样不同磨损时间下的磨损体积。从表2中可以清楚地看到,单一处理和双重处理后试样的磨损量明显低于未表面处理试样。当磨损9h时,未表面处理试样的磨损量是单一处理试样的14倍左右,是双重处理试样的23倍左右。很明显,经表面处理后试样耐磨性都得到了提高,特别是经过双重处理的耐磨性更好。
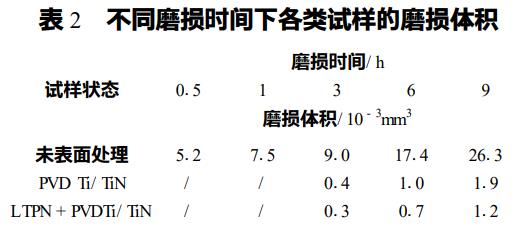
图4、5、6是三种试样磨损形貌的低倍照片及SEM细节,可以看出未表面处理试样磨损形貌为典型的犁沟(见图4a),而且高倍的SEM照片也显示了严重的犁沟(见图4b),而经表面处理的试样磨损形貌都为非常光滑的表面,即无明显的塑性流动、微裂纹和脆性的迹象(见图5和图6)。
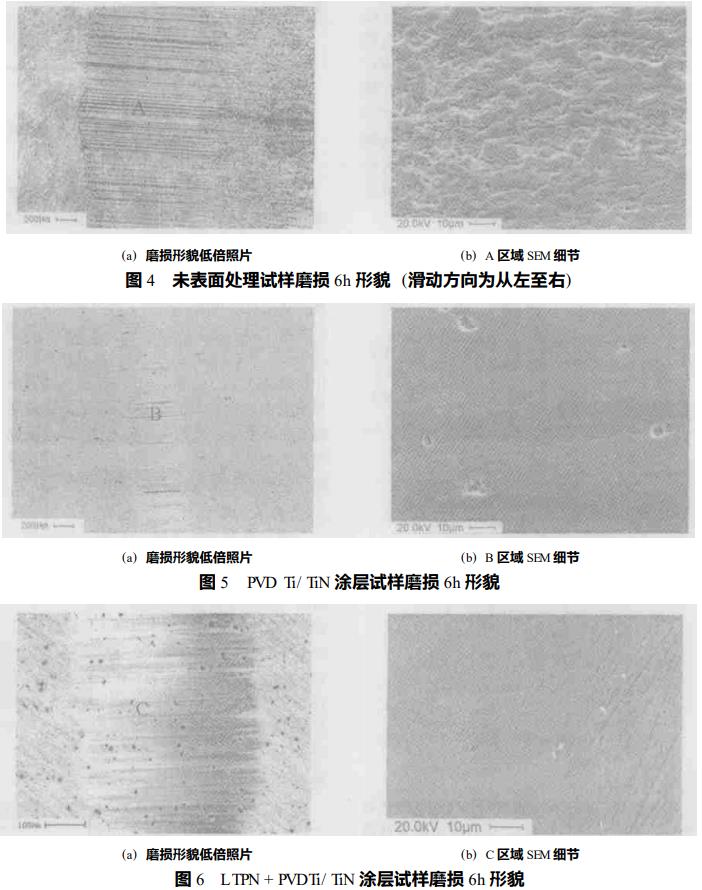
通常,材料的硬度越高,耐磨粒磨损性能越好。在滑动磨损试验过程中,未表面处理试样的Ha/Hm值(这里Ha指对磨试样表面硬度,Hm指上试样表面硬度)约为1.5左右,因此按M.M赫鲁晓夫的结论,试样会产生严重的平行于滑动方向的犁沟,同样,对于表面处理过的试样,Ha/Hm约为0.4,对磨试样硬的粗糙峰对上试样只是起到抛光作用,所以,试样显示出比较光滑的磨痕。而且从磨损形貌看(图5b和图6b),双重处理显示比单一处理更光滑的磨损表面,这主要归因于离子氮化提高了材料的表面承载能力和涂层与基体的结合强度,降低了磨损过程中表面和次表面的剪切变形,使涂层在一定外加载荷冲击作用下不易剥落而造成三体磨粒磨损。
3.4 应用试验
对经PVD Ti/TiN单一处理的模具进行了实际应用试验,该冷冲模具实际使用寿命由原来的约2500次增加到6650次,即模具实际使用寿命提高了2倍多,而且从模具磨损后的失效形貌发现磨损部位为光滑的表面,属于逐渐磨损,没有出现涂层剥落的痕迹,这与试样的磨损试验结果相一致。
4、结论
(1)在Cr12MoV钢上沉积Ti/TiN涂层能显著地提高Cr12MoV钢的表面硬度及承载能力。而且,先进行低温等离子氮化处理的双重处理更能改善涂层-基体结合条件,显著提高涂层与基体的结合强度,这归因于Ti/TiN涂层强化和韧化的作用以及中间氮化层的强化作用。
(2)硬、韧和低摩擦系数的Ti/TiN涂层大大地提高了Cr12MoV钢的耐磨性,与未经表面处理试样比较,单一处理和双重处理试样磨损形貌都为比较光滑的表面,而且在磨损时间相同的条件下,双重处理比单一处理有更少的磨损量。
声明:本站部分图片、文章来源于网络,版权归原作者所有,如有侵权,请点击这里联系本站删除。
返回列表 | 分享给朋友: |